In the welding industry, a significant challenge is the scarcity of skilled talent. Traditional welding techniques like TIG and MIG often require years of experience to master. However, modern advancements, particularly handheld laser welding, offer a solution that can be learned in weeks, not years. This article, authored by Joe Dallarosa, explores the fundamental differences between traditional welding methods and laser welding, helping welders understand how this modern technique can enhance productivity and profitability.
Modern Options for Welding: Photons vs Electrons
Many traditional welding processes use electricity, or electrons, to achieve fusion between metal parts. These processes include Electron Beam Welding (EB), Gas Tungsten Arc (TIG), Shielded Metal Arc (SMAW), Gas Metal Arc (MIG or MAG), Atomic Hydrogen Welding, Spot Welding, Plasma Arc, Carbon Arc, and Drawn Arc (Stud Welding), among others. This article explores the basic differences between laser welding with photons versus electrons.
Traditional Welding Techniques
The process of traditional welding with electrons requires a source of voltage, which can be either AC or DC. The source provides the necessary current for the thickness of the material to be welded. These electrons are delivered to the workpiece via a powered electrode, which can be a tungsten tip (TIG), a metal wire (MIG), or a flux-coated rod (SMAW). The workpiece must also be connected to an electrical ground for the current to flow.
The principle of electron welding is simple: an electrical arc bridges the electrode with the workpiece, resulting in a flow of an electrical current (electrons) creating plasma. This plasma and current flow produce a molten weld pool, which joins the two parts as it solidifies as the arc advances (travels).
This molten pool can approach a temperature of 4530°F (2500°C) and needs to be protected from the oxidizing atmosphere with shielding gas such as Nitrogen, Argon, or Helium. Modern welding machines are equipped with precise current control, radio frequency modulation to initiate and stabilize the arc, pulsed arc functionality, and other features to facilitate achieving quality welds.
Challenges in Traditional Welding
It should be noted that DC electron welding generates a magnetic field which can disturb the arc and cause it to not flow the shortest distance to the workpiece. This can lead to inconsistencies in the weld bead, such as splatter and porosity. Since the current in AC is alternating, this has little effect on producing a magnetic field. DC processes are generally preferred by welders as they produce a more controllable arc, resulting in less splatter and better-looking weld beads.
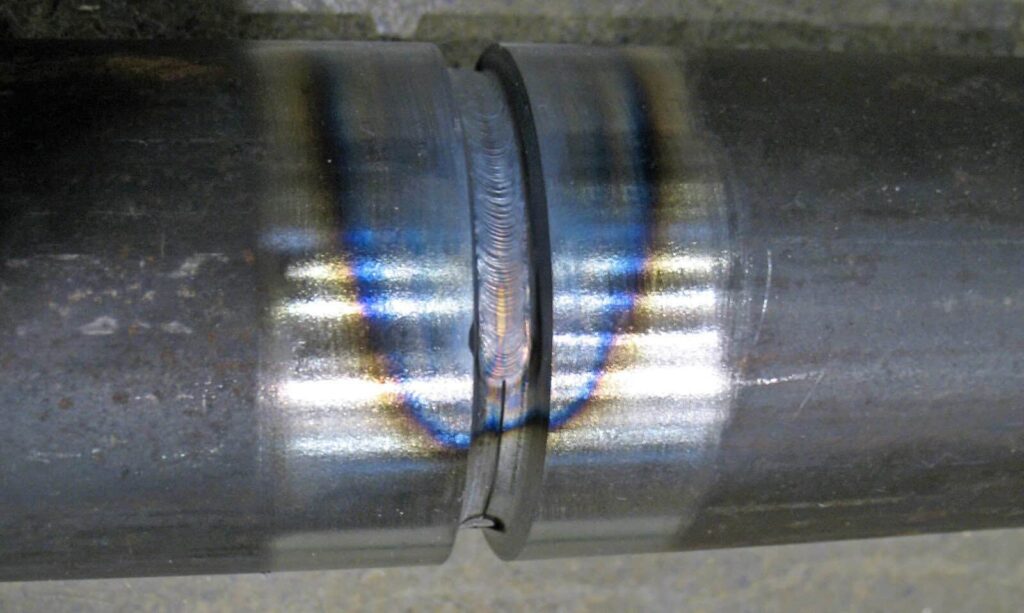
Traditional welding processes produce a large Heat Affected Zone (HAZ), causing changes in the surrounding material’s properties. This can lead to multiple areas with different characteristics, affecting the weld quality and strength.
Laser Welding – A modern alternative
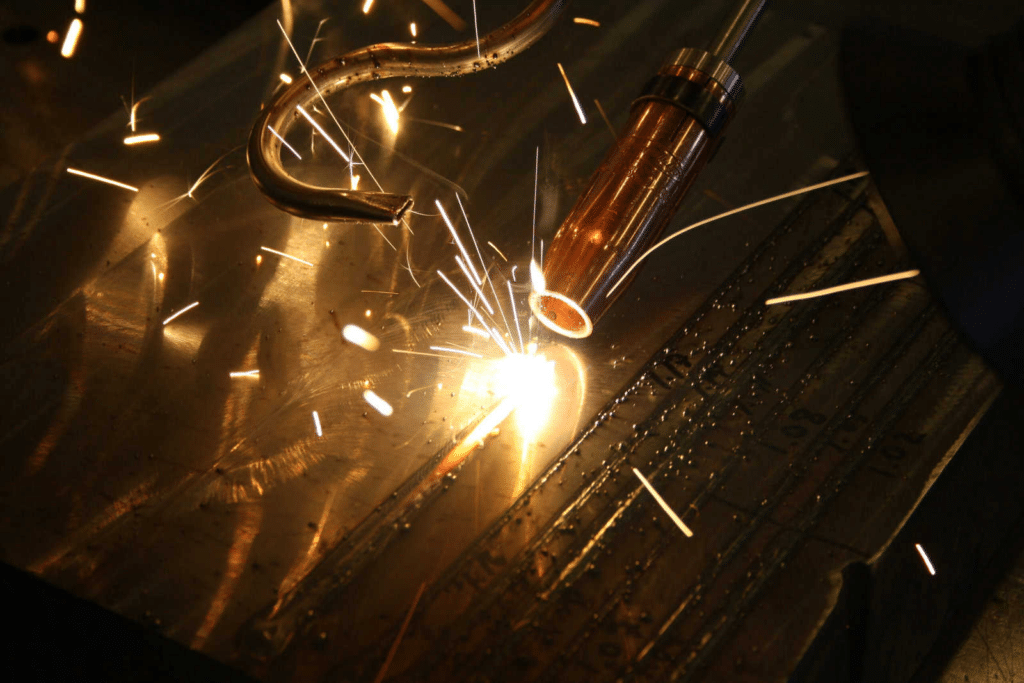
Laser welding represents a modern alternative to traditional methods, offering precise and efficient results. The first working laser was brought into reality in 1960 by Theodore Maiman. In just over six decades, lasers have become an integral part of modern infrastructure. Odds are, you’re either directly or indirectly using a laser right now to read this article. Using a laser involves several different characteristics of light such as wavelength (color), power, laser spot size and either using the laser in a Continuous Wave (CW) or in a pulsed mode changing the repetition rate and pulse width (how long the light is on during a given cycle).
Laser welding requires a source of photons which can be delivered to a workpiece by laser diodes directly, or by channeling laser light through a fiber (known as “pumping”) that is doped with a material that will produce the specific laser light for the application. This light (photons) is then transmitted through a glass fiber and then through a series of lenses where it is focused onto the material. This light is in the infrared part of the spectrum where the laser light produced is both efficient to produce and can be absorbed by some metals. Imagine using a magnifying glass to start a fire with the sun – laser welding works via the same concept.
Types of Laser Welding
Heat Conduction Welding
This process uses focused light to heat the material near the surface, creating a weld pool that quickly cools and solidifies, joining the parts. The energy from the photons enters the weld zone by heat conduction, producing a smooth, aesthetically pleasing, and precise weld.
Deep Penetration/Keyhole Welding
This process uses a narrow beam of focused light to create a deep, narrow channel of molten material. Metal vapor is released as a byproduct of this extreme amount of energy hitting the workpiece and creating a cavity in a matter of milliseconds. This vapor-filled cavity is known as the keyhole, which fills with molten metal as the laser advances (travels). This type of welding produces a narrow channel of welding that can be used on materials with thicknesses of half an inch or greater.
Advantages of Laser Welding
Laser welding has been documented to be up to 10 times faster than conventional electron welding. It produces a small spot of concentrated light with a power density close to 10MW/cm² (1.6MW/in²), resulting in a smaller Heat Affected Zone. This offers clear advantages in weld strength, appearance, and integrity. Additionally, laser welding can be learned quickly, addressing the industry’s talent shortage by enabling new staff to become proficient in weeks instead of years.
Conclusion
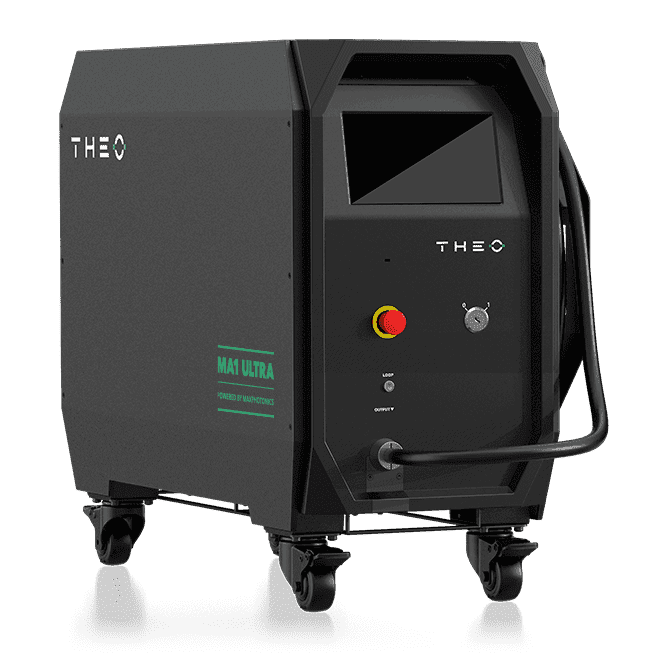
Laser welding offers numerous benefits over traditional welding methods, including increased efficiency, precision, and reduced training time. By transitioning to laser welding, companies can address the talent shortage, improve productivity, and enhance profitability. A particular advancement in this field is handheld laser welding, which combines the precision and efficiency of traditional laser welding with the flexibility and ease of use needed in various work environments. Handheld laser welders, like the Theo MA1 Laser Welding Machine, are ideal for tasks that require mobility and versatility, making them an excellent choice for modern welding needs.
Stay informed about the latest advancements in welding technology by signing up for our newsletter. Receive updates, tips, and expert insights directly to your inbox. Sign up below.