Explore handheld laser welding with THEO's application specialist Harrison Shoup. Understand key considerations for integrating this technology, from equipment costs to safety setup. This guide offers insights into laser welding's benefits and challenges, providing a straightforward view on its role in modern manufacturing and safety.
The Evolution of Handheld Laser Welding
Laser welding was first achieved in a lab setting more than fifty years ago, yet it has only been within the last decade that handheld laser welding tools have been introduced to the general commercial marketplace. Having been developed to support NASA engineers and technicians in the maintenance and repair of spacecraft, handheld fiber laser welding presents unique advantages and challenges for those wanting to integrate this technology into their workspace.
Cost: The Primary Barrier to Entry
Initial cost is generally the first consideration in choosing to make the switch to laser welding. While the Internet will yield many grey market options that can be had for several thousand USD, buyers may find themselves out of luck when these machines malfunction or they run out of consumables. After-sales support can be questionable if available at all. Some of these units may also be missing key safety components required by industrial, state, and federal guidelines – raising serious liability concerns should the use of said equipment result in a recordable injury.
“Navigating the transition to laser welding demands more than just an investment; it requires a commitment to safety and innovation.”
– Harrison Shoup, THEO’s Application Specialist
Professional Grade Equipment: A Worthwhile Investment
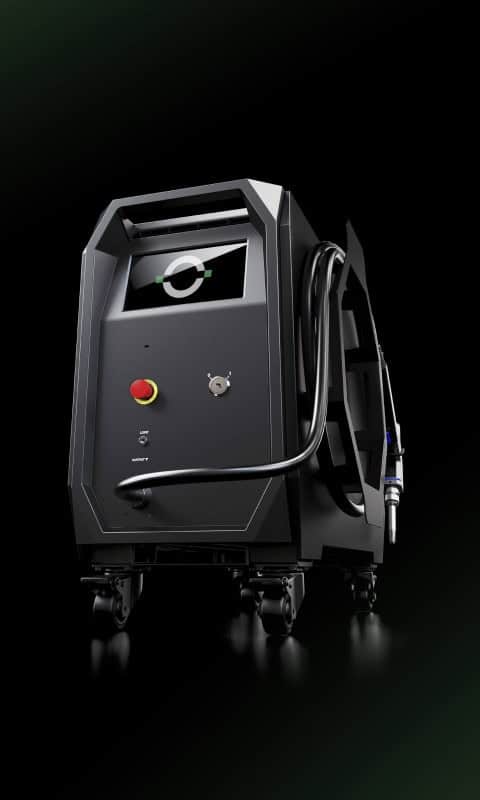
Professional grade handheld laser welding machines such as the THEO MA1 series come with a higher purchase price. The added value comes in the form of access to a global support network of engineers and technicians as well as documented safety certifications from ISO, ANSI, and the FDA mean end users can feel confident relying on these machines to provide years of reliable and safe operation, with minimal (if any) interruption in the event of a safety audit by any regulatory agency.
Creating a Laser Safe Workspace
In addition to the cost of laser welding equipment itself, a budget will need to be set aside to establish and construct or convert a laser safe area within the workspace. Class 4 lasers, the type of which are powerful enough to weld quarter-inch thick steel in a single pass, can pose multiple serious health and safety risks to everyone in the work area during welding operations. Beyond the risks of thermal injuries and metal fume exposure presented by all thermal welding processes, the Class 4 beam itself can cause permanent, irreversible damage to the human eye. In some extreme cases, even just the reflected light of this beam bouncing back off the workpiece or nearby reflective surfaces can send dangerous amounts of Infrared radiation into the surrounding workspace. The laser welding area needs to be either completely lightproof to the outside, or protected by specifically formulated Infrared safety material that can absorb the hazardous, invisible Class 4 beam. Proper use of federally mandated safety interlocks and laser-specific PPE must be implemented and enforced to achieve safe laser welding standards in any workplace. (Learn more about Safety in Laser Welding at THEO ACADEMY)
The Advantages of Filler-Free Welding
In contrast to MIG and TIG processes which rely on electrons being passed through filler wire to fuse parts, one of the strongest arguments for the modern handheld laser welding process is the potential for an end user to achieve their welding goals without the use of filler. The welding laser beam is directed, or “wobbled” by a moving mirror within the hand torch dozens or even hundreds of times per second over the weld joint, melting down base material on both sides and whipping the two molten edges together to achieve a very narrow, very consistent fusion weld bead. Due to the rapid thermal input but tiny heat affected zone achieved by the laser welding process, great improvements to travel speed and aesthetic quality of most welds on sheet metal 4mm thick and below will be observed. Depending on material and thickness, the handheld laser welding process can deliver comparable results up to four times faster as a manual MIG or TIG process on the same material and joint design.
Reduced Training Time and Post-Processing
Because the handheld laser welding process requires no weaving of the torch by hand, achieving near-perfectly consistent bead appearance is a matter of maintaining steady travel speed along the length of the joint. Spatter is largely a non-issue – some reflective materials will result in minor spatter due to reflectivity combined with shielding gas, but chisels and wire wheels are tools that remain largely untouched once the switch to laser welding has been made within a workshop. Post processing time budgets can be cut down significantly – possibly eliminated in some cases. Of course, these advantages in welding ease also mean the time to train someone to achieve consistent high-quality results with a laser welding device is greatly reduced, compared to achieving the same level of competency and consistency with a traditional hand welding process.
Expanding Capabilities with Laser Welding
Going beyond the advantages posed to general welding and production work, the handheld laser welding process brings with it new possibilities in welding super thin components, integration with high speed automated solutions, and joining parts of differing thicknesses. As the technology grows, researchers and end users continue to innovate and find novel uses for the versatility offered by a laser tool which can be programmed to weld over half a dozen alloys natively, at thicknesses ranging from ten thousandths of an inch up to a full quarter inch with a single pass. Theo’s MA1 units, for example, arrive with preinstalled welding parameters encompassing fusion and wire assisted programs across five different alloys, with options for thickness ranges from under 1 millimeter to over 6 depending on material and joint design. Additionally, the end user can overwrite these settings at any time with their own adjustments, or make use of 32 blank program slots to save their custom weld settings. All of these options are available through an easy to understand, touchscreen-based User Interface.
“Handheld laser welding is not just a tool, it’s a revolution in how we approach precision and efficiency in the workspace.”
– Harrison Shoup, THEO’s Application Specialist
The Future of Handheld Laser Welding
After maintaining a small-yet-growing place in the welding world over roughly half a decade, handheld laser welding is still firmly in the hands of early adopters. Between initial budget and safety considerations, many prospective users may hesitate to invest in this relatively new technology. With that said, as more and more advantages and applications of this process continue to be discovered and improved upon, it’s hard to deny the reality of laser welding’s expanding role in the areas of modern manufacturing and fabrication processes.